Need to create a complete compliance solution for your team?
Read our series and learn how with ICC!
- Most Recent
- Regulations
- Popular Topics
- Frequently Asked Questions
- Webinars
- Catalogs
- Downloadable Resources
- Past Newsletters
Most Recent
Hazmat Driver Requirements
Hazmat Driver Requirements A frequently asked question on our helpdesk related to a hazmat driver. What is a hazmat driver?...
Why are SDS so Important?
Why are SDS so Important? Everybody loves those quartz countertops in their kitchens and bathrooms. Did you know there are...
Extracting a Solution – A New Description for Hazardous Extracts
Extracting a Solution – A New Description for Hazardous Extracts If you’ve spent much time in biology class, you may...
Addendum to IATA’s 65th Edition
Addendum to IATA’s 65th Edition Congratulations, you’ve purchased the latest edition of the International Air Transport Association (IATA) regulations –...
Crimp it! Crimp it Good!
Crimp it! Crimp it Good! Whether it is taping, torquing, or friction, there are many ways to properly close a...
All About Torque
All About Torque Whether you are using combination or single UN packaging, closing instructions are an essential piece to the...
Regulations
Hazmat Driver Requirements
Hazmat Driver Requirements A frequently asked question on our helpdesk related to a hazmat driver. What is a hazmat driver?...
Why are SDS so Important?
Why are SDS so Important? Everybody loves those quartz countertops in their kitchens and bathrooms. Did you know there are...
Extracting a Solution – A New Description for Hazardous Extracts
Extracting a Solution – A New Description for Hazardous Extracts If you’ve spent much time in biology class, you may...
Addendum to IATA’s 65th Edition
Addendum to IATA’s 65th Edition Congratulations, you’ve purchased the latest edition of the International Air Transport Association (IATA) regulations –...
Crimp it! Crimp it Good!
Crimp it! Crimp it Good! Whether it is taping, torquing, or friction, there are many ways to properly close a...
All About Torque
All About Torque Whether you are using combination or single UN packaging, closing instructions are an essential piece to the...
Popular Topics
Hazmat Driver Requirements
Hazmat Driver Requirements A frequently asked question on our helpdesk related to a hazmat driver. What is a hazmat driver?...
Why are SDS so Important?
Why are SDS so Important? Everybody loves those quartz countertops in their kitchens and bathrooms. Did you know there are...
Extracting a Solution – A New Description for Hazardous Extracts
Extracting a Solution – A New Description for Hazardous Extracts If you’ve spent much time in biology class, you may...
Addendum to IATA’s 65th Edition
Addendum to IATA’s 65th Edition Congratulations, you’ve purchased the latest edition of the International Air Transport Association (IATA) regulations –...
Crimp it! Crimp it Good!
Crimp it! Crimp it Good! Whether it is taping, torquing, or friction, there are many ways to properly close a...
All About Torque
All About Torque Whether you are using combination or single UN packaging, closing instructions are an essential piece to the...
FAQs
DG / HazMat Industry Acronyms
DG / HazMat Industry Acronyms Have you ever spoken with a seasoned Hazmat professional who is seemingly talking in gibberish??...
Free Regulatory Webinars
Our Quarterly Webinar Series, created by ICC Regulatory Experts, reports on recent or pending regulatory changes that impact your business. Our webinars are available to registered customers or subscribers.
Subscribe to our newsletter for details about upcoming webinars and ongoing industry news.
Sign Up
Sign In
Free Regulatory Catalog
For over 30 years, ICC Compliance Center has been providing customers with high quality regulatory products, services, and training for customers storing or transporting dangerous goods. Please feel free to browse through our catalogues to learn more about how we can empower your team with the right tools and knowledge to safely handle dangerous goods.
For ongoing insights and informative articles, subscribe to our newsletter!
Sign Up
Sign In
Downloadable Resources
For over 30 years, ICC Compliance Center has been providing customers with high quality regulatory products, services, and training for customers storing or transporting dangerous goods. Please feel free to browse through our catalogues to learn more about how we can empower your team with the right tools and knowledge to safely handle dangerous goods.
For ongoing insights and informative articles, subscribe to our newsletter!
Sign Up
Sign In
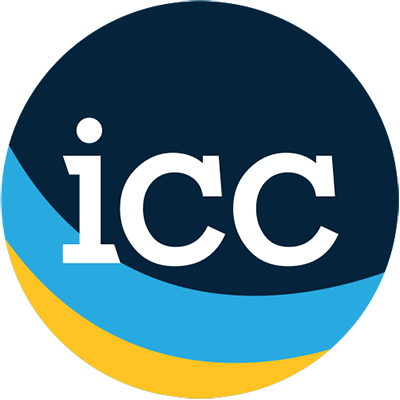